Ottimizzazione della distribuzione degli spessori
Le novità di OptiAssist per Simcenter 3D v3.0
- 44 minuti
- 1 Video
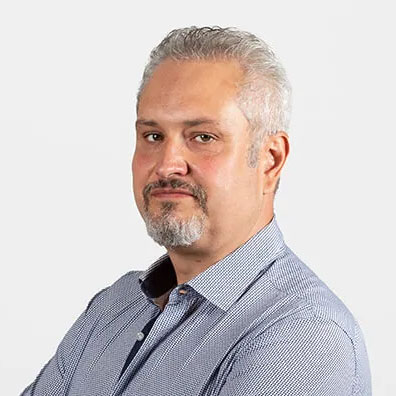
Ing. Francesco Palloni
SmartCAE
PARTNER
Descrizione Webinar
Quando il modello strutturale è realizzato con elementi SHELL nasce spesso la volontà di ottimizzare la distribuzione degli spessori per inseguire gli obiettivi di peso, di rigidezza e di frequenze di risonanza.
Eseguire questo tipo di studio manualmente è un’operazione tediosa e che può richiedere numerose iterazioni prima di ottenere un disegno che rispetta tutte le condizioni.
In questo episodio vedremo come OptiAssist aiuti a ricavare automaticamente la distribuzione degli spessori per parti realizzate con lamiera metallica e per prodotti stampati in plastiche.
Questo è il secondo episodio della serie dedicata a OptiAssist per Simcenter 3D.
Il primo episodio è dedicato alla tecnologia RDM acronimo di Reinforcement Derivation Method, una tecnologia basata sull’ottimizzazione topologica che permette di individuare facilmente la posizione migliore dove introdurre rinforzi per irrobustire una struttura esistente.
Il terzo invece riguarda l’ottimizzazione delle strutture in composito nel rispetto dei vincoli tecnologici e di manufacturing. Questa è una caratteristica unica di OptiAssist che lo ha reso molto popolare sia tra i team di Formula 1 che tra quelli di Coppa America.
Oggi, invece affrontiamo un tema che è quello dell’ottimizzazione delle strutture di piccolo spessore modellate con elementi shell. Possono essere parti a spessore costante, come lamiere o geometrie a spessore rastremato, come parti stampate in plastica.
Durante questo seminario avremo modo di vedere in azione OptiAssist sia con l’uno che con l’altro tipo di struttura.
OptiAssist è un prodotto sviluppato da GRM Consulting, una società inglese. Per la realizzazione di OptiAssist GRM Consulting aveva l’obiettivo di sviluppare un ambiente unificato che permettesse agli utilizzatori di Simcenter 3D di sfruttare al massimo il potenziale messo a disposizione dal modulo Nastran Optimization, ovvero il modulo SOL 200 del solutore Nastran. Per raggiungere questo obiettivo GRM ha lavorato in due ambiti, il primo è stato quello di semplificare l’interfaccia grafica per pilotare la SOL 200 rendendola meno complicata e quindi accessibile anche a chi ha meno esperienza per quanto riguarda l’utilizzo dei software di ottimizzazione, tra cui, ad esempio, i progettisti. In questo modo l’ottimizzazione strutturale può essere utilizzata in maniera efficace anche nelle fasi preliminari del progetto. Il secondo aspetto è stato quello di portare sulla piattaforma di Simcenter e Nastran l’esperienza maturata con il solutore Genesis, che è un solutore allo stato dell’arte per quanto riguarda i temi dell’ottimizzazione struturale. Ad esempio, tutta la suite di strumenti per l’ottimizzazione dei compositi che vedremo nel prossimo episodio e tante altre tecnologie che vediamo, alcune di queste, anche oggi, per ad esempio partizionare i modelli FEM esistenti.
OptiAssist per Simcenter 3D è arrivato adesso alla terza versione, quindi è un software robusto, maturo, affidabile che si integra alla perfezione con l’ambiente di modellazione di Siemens. Come dicevo uno dei punti di forza, forse il principale punto di forza per Simcenter 3D è la sua semplicità di utilizzo. Il programma viene integrato nell’interfaccia utente di Simcenter attraverso un ribbon dedicato, lo vediamo qua in questa slide, che contiene in maniera organizzata tutte le funzioni di ottimizzazione. Nella prima parte sono presenti i vari moduli di ottimizzazione, categorizzati per tipo, ottimizzazione degli spessori, ottimizzazione topografica, ottimizzazione freeshape, ottimizzazione dei compositi e RDM che abbiamo visto la volta scorsa. Cliccando su ogni pulsante viene attivato un Wizard che propone una serie di pannelli, un percorso guidato con il quale l’utilizzatore, rispondendo a delle domande, riesce a mettere in piedi un progetto di ottimizzazione in maniera molto rapida. Quindi può definire quelli che sono gli obiettivi, i vincoli, vincoli come possono ad esempio essere il valore della massa da rispettare o vincoli tecnologici come piani di simmetria o cose di questo tipo. Dopodiché nel ribbon troviamo il pulsante per lanciare l’ottimizzazione, una volta eseguito il run di ottimizzazione ci sono gli strumenti per interrogare rapidamente i risultati e interpretare appunto, prendere decisioni sul progetto in base ai risultati dell’ottimizzazione. Questa impostazione permette di semplificare l’utilizzo sia per chi già conosce NX Nastran e Simcenter 3D e riduce la rampa di apprendimento necessaria per un nuovo utilizzatore quando si vuole mettere a punto uno studio di ottimizzazione robusto e affidabile.
La prima parte è, il punto di partenza dell’ottimizzazione è un modello agli elementi finiti realizzato con elementi shell ai quali vengono assegnati gli spessori di primo tentativo sulla base dell’esperienza, viene seguito il calcolo agli elementi finiti e sulla base dei risultati vengono verificate le prestazioni. Se le prestazioni non sono in target, non sono in obiettivo, l’analista deve interpretare i risultati e usando l’esperienza e talvolta, se si sta analizzando qualcosa di completamente nuovo anche l’intuito, decidere sia in quali zone andare a modificare gli spessori che il valore di spessore da assegnare alle varie zone. Dopodiché si aggiorna manualmente il modello e nasce un loop di iterazioni che tipicamente possono richiedere, in alcuni casi anche decine di cicli, prima di raggiungere l’obiettivo e poter deliberare il progetto. Pertanto si tratta di un processo iterativo che richiede tempo per essere completato, di un processo basato molto sull’esperienza e sull’intuito di chi sta utilizzando il software e di un processo manuale, pertanto soggetto a possibili errori.
Vediamo adesso come gli algoritmi di ottimizzazione e la matematica possono aiutarci a rimuovere tutte e tre queste limitazioni.
Una delle tecniche di ottimizzazione più diffuse, che è quelle implementata anche nella SOL 200 di Nastran è il metodo del gradiente, noto anche come metodo della sensitività. Di fatto il punto di partenza è sempre lo stesso, prima viene fatta l’analisi agli elementi finiti, con la differenza che si definiscono delle funzioni obiettivo che vengono espresse in una formula di cui vogliamo andare a trovare il minimo.
Ad esempio, se vogliamo massimizzare la rigidezza di una struttura, l’ottimizzatore cercherà di minimizzare la cedevolezza.
Calcoliamo poi con veri metodi numerici, differenze finite, sviluppi in serie di Taylor, formule analitiche, la variazione della funzione obiettivo, come ad esempio la cedevolezza, al variare di ciascuna variabile di progetto, nel nostro caso gli spessori.
Il software interpreta le derivate in maniera da identificare un nuovo set di valori di spessori e aggiorna il modello rilanciando nuovamente l’analisi. In ogni iterazione viene verificato che il nuovo disegno non sia in conflitto con eventuali vincoli da rispettare, come ad esempio la massa complessiva del sistema. Dopodiché questo ciclo viene iterato in maniera automatica finché non si raggiunge l’obiettivo e la procedura si ferma con un disegno che rispetta le prestazioni desiderate.
Questo è uno degli approcci implementati nei software di ottimizzazione presenta vari vantaggi rispetto al metodo manuale. Il primo è che posso definire chiaramente l’obiettivo dello studio e dei vincoli geometrici di vario tipo che il progetto, il modello FEM deve rispettare. Essendo un metodo basato sulla sensitività, l’algoritmo capisce da solo quali siano gli spessori più influenti e quali invece possano essere da parte. Pertanto aiuta il progettista anche a capire il comportamento strutturale del prodotto e fornisce delle informazioni utili anche per progettare eventualmente una versione successiva del prodotto. È un metodo numerico, che si interrompe automaticamente quando ha raggiunto la convergenza, nel caso in cui non la raggiunga possiamo comunque fissare il numero massimo di iterazioni e vedere dove è arrivato l’algoritmo, per cui alla fine otteniamo sempre dei risultati che ci aiutano a comprendere il comportamento del sistema.
In ultimo, si tratta di una procedura automatica, in cui tutte le scelte vengono fatte a monte e che non richiede un intervento manuale dell’operatore durante la sua esecuzione, se il risultato per qualche motivo non ci soddisfa è sufficiente cambiare le impostazioni con cui abbiamo lanciato l’ottimizzatore e rilanciare poi l’analisi, per eventualmente saggiare e provare varie opzioni progettuali.
Quali sono i vantaggi di OptiAssist per Simcenter 3D sia rispetto agli approcci manuali che ad altri software di ottimizzazione?
Il primo è legato alla semplicità con cui si fanno questi studi, quindi la semplicità d’uso, l’interfaccia utente. Ogni tipo di ottimizzazione dentro OptiAssist viene impostato attraverso un Wizard che guida l’utente nel definire tutti gli aspetti dello studio. Lo scopo è proprio quello di rendere fruibile e facilmente accessibile l’ottimizzatore SOL 200 da parte anche di un progettista.
Altra cosa, durante la definizione dello studio l’utente può impostare vari tipi di vincolo che l’ottimizzatore deve rispettare, dal valore della massa a vincoli geometrici, come eventualmente simmetrie. In questa maniera è più semplice per il progettista ottenere risultati che possano essere poi implementati sul prodotto.
Un’altra funzione molto interessante che abbiamo visto in azione sia nel modello della fioriera che nel modello dello sgabello è quello del partizionamento del modello. Supponiamo ad esempio che l’utente abbia creato la struttura di una macchina in carpenteria elettrosaldata, dove tutte le lamiere hanno il solito spessore, in questo caso è molto probabile che abbia utilizzato un solo collector, una sola proprietà per indicare lo spessore di tutti gli elementi. In questo caso diventerebbe complicato andare a segnare spessori differenziati alle varie lamiere, con OptiAssist invece ci sono gli strumenti di raggruppamento automatico, come quello che abbiamo visto in questo caso o quello dello sgabello, con il quale è il software che va a partizionare le patch per poter poi andare a modificare lo spessore localmente. Altra cosa importante, la facilità con cui viene aggiornato il modello agli elementi finiti, in questo caso con gli spessori degli elementi, aggiornati in base all’ultima iterazione dell’ottimizzatore. Questo modello poi può essere utilizzato o nel contesto di un assieme più grande o può essere usato semplicemente per verificare le prestazioni della parte sotto l’azione anche di altri carichi o fare analisi dinamiche o analisi di altro tipo.
Tutto questo si traduce per l’azienda in una drastica riduzione di tempi di sviluppo e costi di realizzazione del prodotto.
Visto che sia lo sgabello che la fioriera sono in materiale plastico è possibile utilizzare l’ottimizzazione per materiali non lineari?
La risposta è no, perché è il metodo del gradiente il metodo basato sulla sensitività che è un metodo basato su un approccio di tipo lineare, per cui non posso introdurre nel modello una risposta di tipo non lineare legata al materiale, ma devo convivere con un’ipotesi di comportamento lineare del materiale. Questo per questo tipo di ottimizzazione, eventualmente dentro Simcenter 3D è presente un altro modulo di ottimizzazione che si chiama HEEDS è un software di ottimizzazione generale multi obiettivo che permette in quel caso di attaccare l’ottimizzazione strutturale a qualsiasi tipo di simulazione, quindi di tipo termico, di tipo non lineare, di tipo fluidodinamico, ma diciamo è un altro strumento.
OptiAssist permette di inserire vincoli legati al processo produttivo o utilizzati per realizzare il pezzo? Stampo plastico, lavorazioni, stampa 3D?
Allora, questo sì, ma non nel contesto dell’ottimizzazione degli spessori. Mi spiego, l’introduzione di un vincolo di produzione, del tipo il componente che viene realizzato per fusione, piuttosto che per stampa 3D, tendenzialmente è argomento di ottimizzazione topologica. Quindi utilizzando il modulo RDM di OptiAssist la risposta è sì, risco a introdurre anche vincoli di produzione, diciamo per esempio nel caso delle fusioni posso imporre una direzione di sformo, per cui il software andrà ad evetare la creazione di sottosquadri rispetto ad un determinato piano di generazione del modello.
Ci sono dei limiti imposti nel numero di variabili di progetto che si possono usare per l’ottimizzazione?
No, diciamo in questo caso rispondo sul tema dell’ottimizzazione degli spessori, non ci sono dei limiti imposti sul numero di variabili ne su quello dei vincoli, gli unici limiti dipendono fondamentalmente dal metodo utilizzato. Il metodo del gradiente è un metodo che richiede l’esecuzione a ogni iterazione del calcolo della matrice di sensitività e del calcolo della risposta del modello. Quindi io aggiorno il modello e poi rilancio per vedere come è cambiata la risposta, per cui se ho un modello leggero come ad esempio il caso della fioriera, gira veramente in pochi minuti tutto il loop di ottimizzazione, viceversa se ho modelli molto grandi con tantissime variabili da controllare i tempi di calcolo si possono allungare proprio a causa della dimensione, della mole del modello. Pero di per se non c’è una limitazione imposta nel numero di variabili e vincoli.